Stained-glass enamel
We create precious tableware in the technique of stained-glass enamel. This is painstaking manual labor that requires jewelry craftsmanship - for example, it took us 4 months of work, 7 jewelers, a team of artists, 2 jewelry techniques, as well as 200 meters of silver wire weighing 100 grams, 17 enamel colors and fire furnaces to create a kovsh based on Russian fairy tales (pictured below).
We talk about the process of creating products from stained-glass enamel...
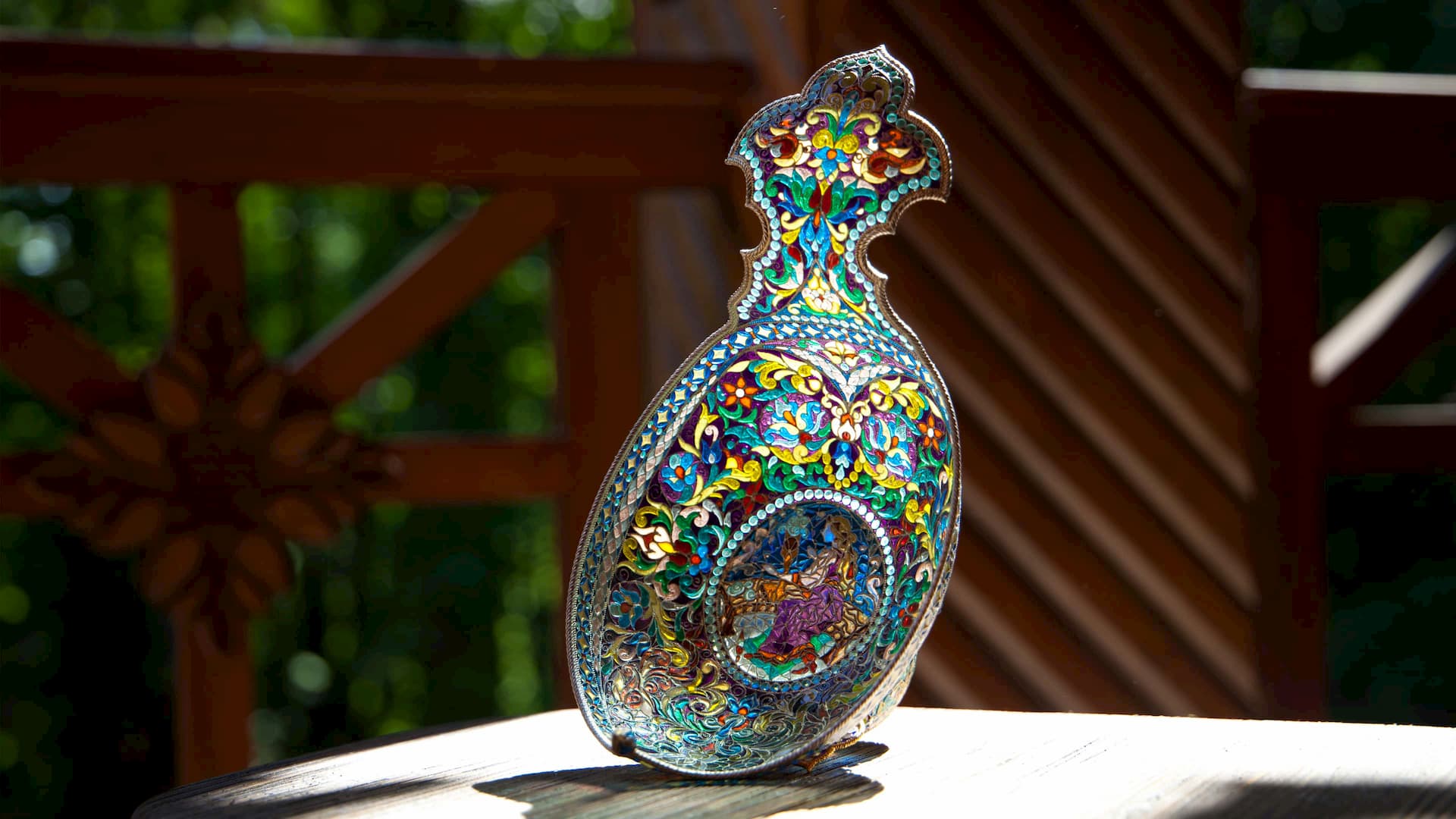
Penetrating through ornate "windows" generously filled with color richness, the sun"s rays are reflected in the water, in the ground, in the air. Warming the created composition of precious metal and glass enamel.
Sketch
It all starts with a sketch ... or rather, a dozen sketches, with a carefully calibrated pattern in accordance with the future shape of the product, with the traditions of Russian ornamentation and the features of the selected jewelry techniques. The artist creates many preliminary sketches, and sometimes the hand only manages to sketch everything that gives birth to consciousness.
First, the plan is drawn in pencil - the size of the product is verified, in accordance with the factors of surface tension of enamels (molten enamel behaves similarly to liquid) and metal, thermal stress and expansion.
Then it's time to look for color solutions. At this stage, the artist takes into account the readability of the overall composition, contrast, light transmittance of the enamel and all that will affect the perception of the future product. An enamel palette is created - only transparent enamels are used. Blind colors are used in the cloisonne enamel technique.
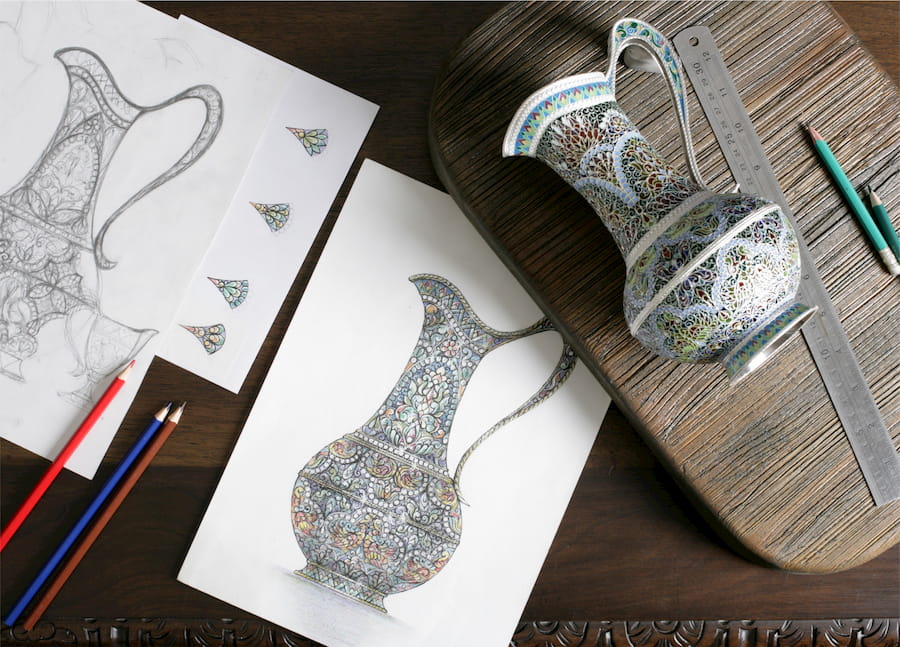
Sketches of a stained-glass jug
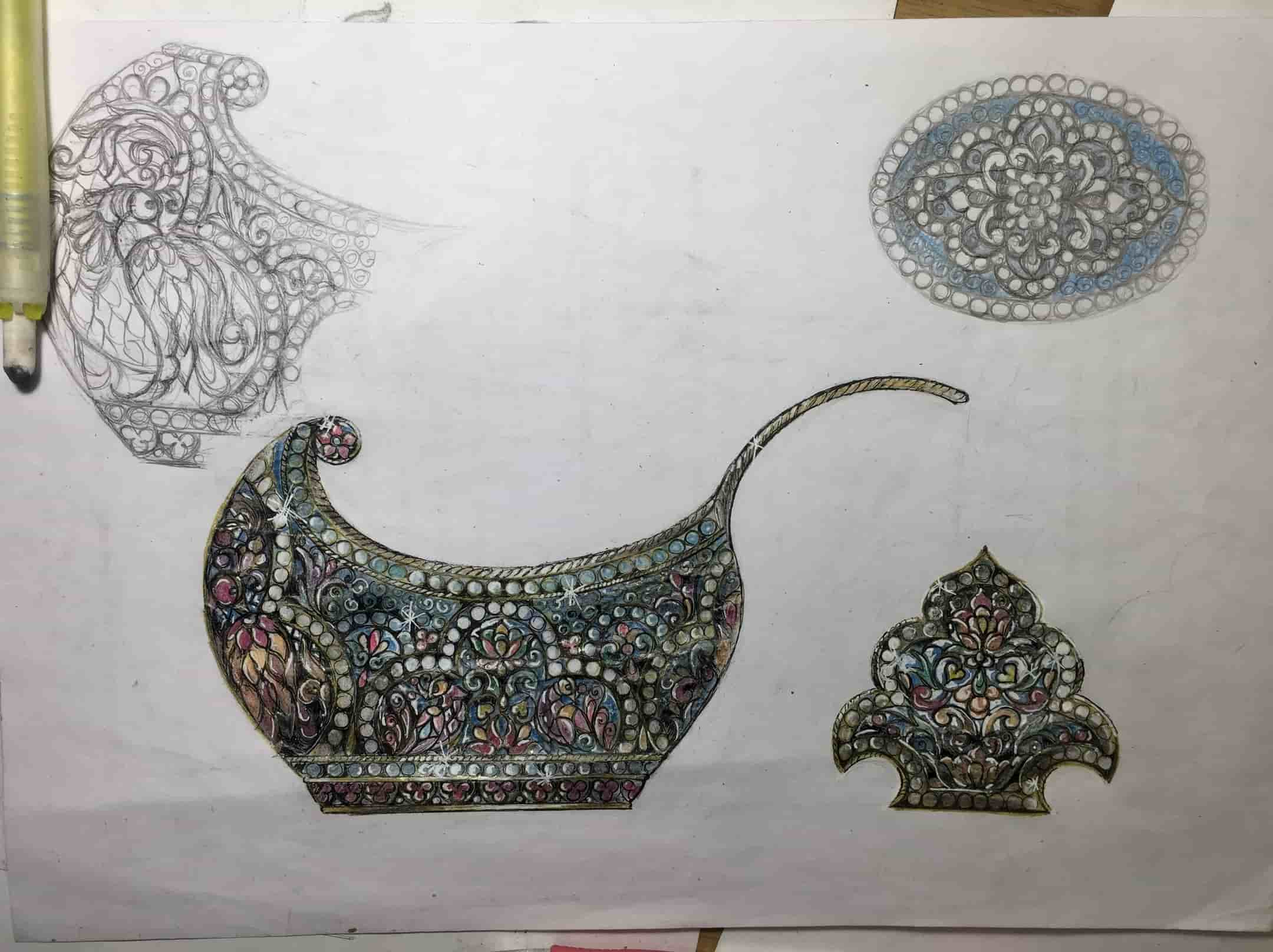
Sketches of a stained-glass kovsh
Jewelry techniques
In choosing jewelry techniques, we were guided by our vision of a fairy tale: stained-glass enamel creates a magical play of light, and silver filigree what adds weightlessness and jewelry is a
silver filigree,
silver filigree, – a silver filigree is a twisted wire folded in half. In a simplified form, the process of creating a filigree looks like this: a wire with a diameter of 0.21 mm is pulled from a bar of silver during rolling and drawing – the massiveness of the future product depends on the diameter of the wire, and since we tried to get the product "airy" and weightless, we settled on the optimal version of the thinnest wire – in this case it will not burn when soldering, and will give a feeling of lightness. A hundred–gram bar of metal makes 200 meters of wire, which we fold in half and twist, forming a twisted thread - we roll it on shafts. The filigree wire is ready.
It is with it that the jeweler works - the master cuts the wire into separate parts and bends and glues the pattern with tweezers, according to the sketch. The whole pattern is sticked together on a tin base, tapped according to the shape of the future kovsh.
However, keep in mind that when soldering, all the glue will burn and the pattern will crumble, sothe metal artist sprinkles each joint of the pattern with silver solder, which melts under the flame, joining together the frame of the product. It turns out the silver base of the future kovsh.
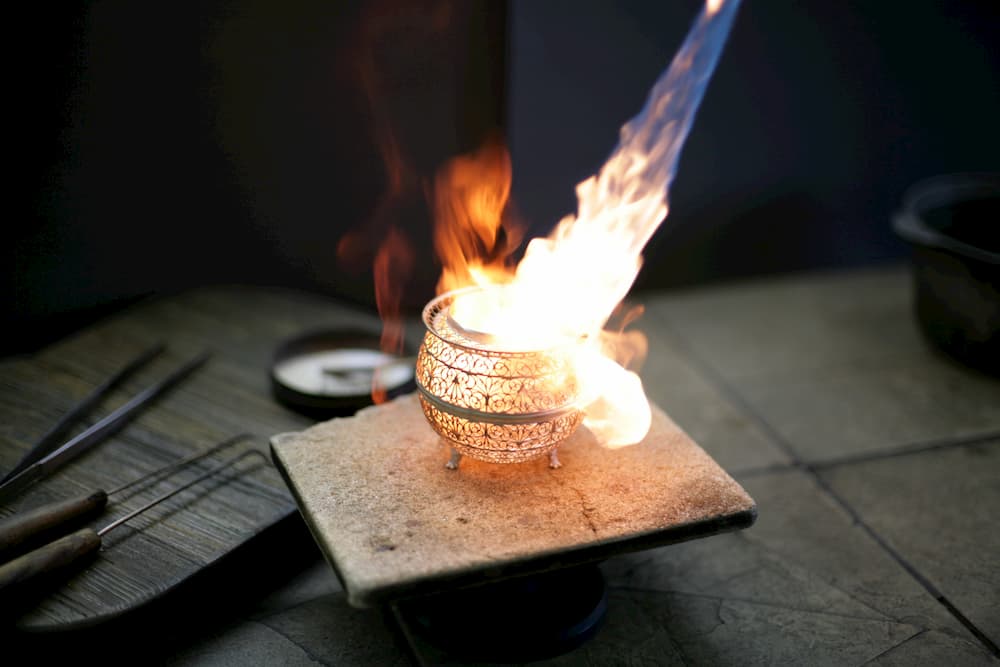
Soldering process
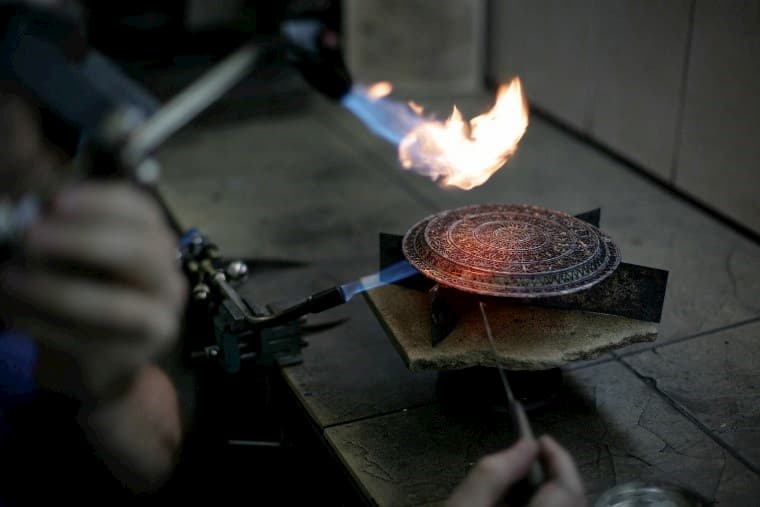
Soldering using solder
Stained-glass enamel
Enamel is a glassy mass (quartz, various fluxes) with metal impurities. The color of the enamel and its properties directly depend on the type of metal and fluxes – it can be both opaque enamel (deaf) and stained-glass enamel. Blind enamel is used in the technique of cloisonne enamels. We are also interested in stained glass enamel, it is also plique-a-jour from the French.
In color, gloss, and iridescence, stained-glass enamel has similarities with precious stones and, moreover, acts as a jewel on an equal basis with them. Stained-glass enamel is one of the most difficult and time–consuming enameling techniques. In the process of work, it can be very unpredictable and even capricious, requiring experience, patience and talent from the master.
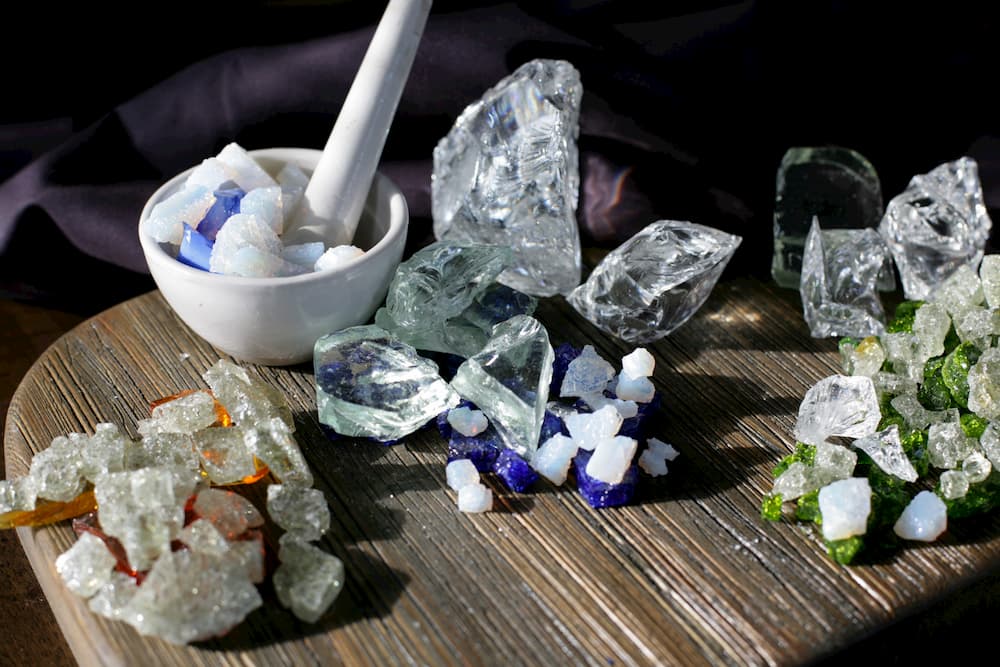
Different enamel colors
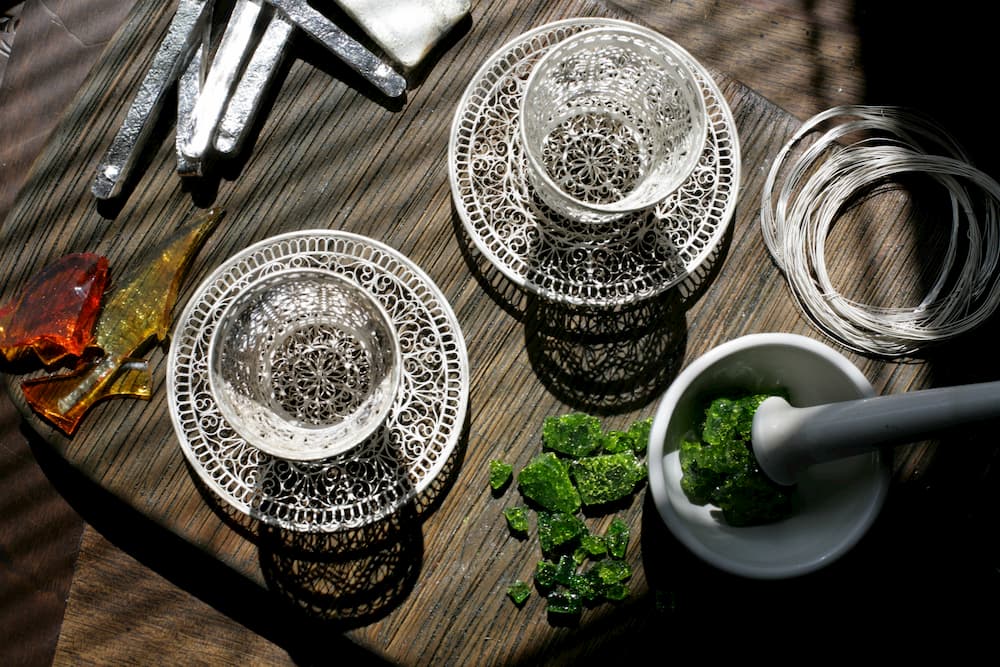
Openwork filigree base
The enamel needs to be prepared - this process consists in grinding, rubbing and then soaking the ground enamel in water. The purpose of this stage is to obtain enamel powder (grains) of the required size, which does not have foreign inclusions. This stage is very important and has many professional secrets.
And finally, one of the most important and amazing stages of work comes, requiring special care - the laying of stained-glass enamel. The enameler puts enamel into each cell of the filigree pattern with a jewelry spatula. You need to be extremely careful not to get on the filigree and not to touch the already embedded enamel.
One of the main difficulties arises from the fact that each color has its own melting point – from 720 to 760 degrees, and we cannot lay all the colors at the same time and burn them. Therefore, the enamel artist starts with the most refractory color. The quality of the enamel, its color and transparency depend on the correct temperature.
The firing process requires a lot of experience, and success depends not only on the master - we never know how the product will behave alone with the fire in the muffle furnace. This is a very exciting moment.
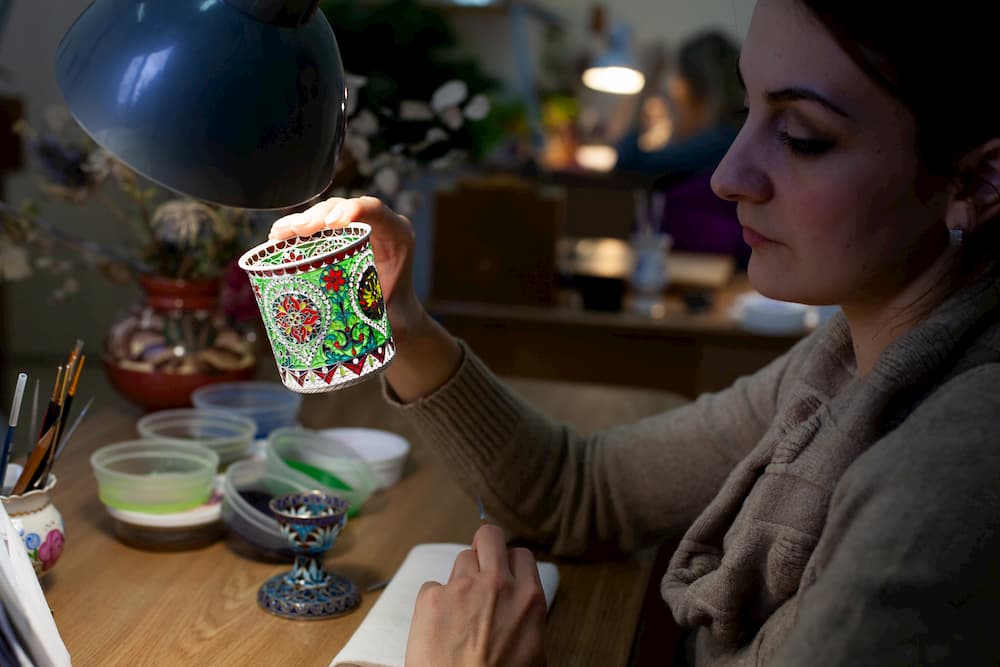
An enamel artist in the process of work
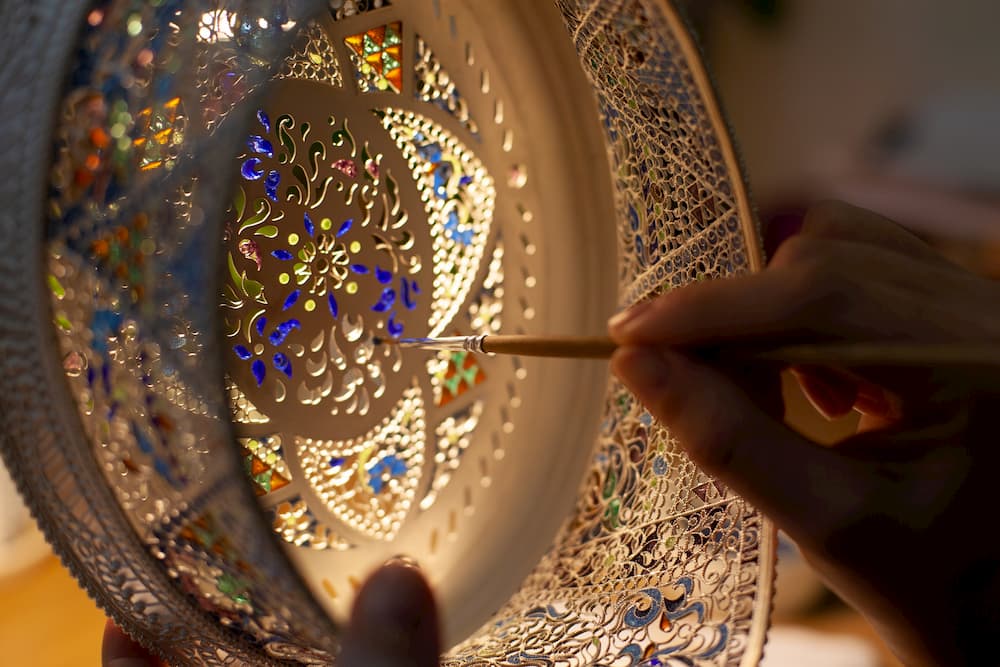
Laying enamels with a brush
After the enamel suspension of the same color is embedded in the cells, the most exciting stage begins – this is firing in a muffle furnace. at a temperature of 760 degrees (for red). The product remains alone with the fire and how the enamel and filigree will behave is unknown. Our task is to control the exact temperature and not "overexpose" the product in the oven, otherwise the enamel will fade.
The number of firing directly depends on the number of enamel colors. The quality of stained-glass enamel depends on the skill of the enamel artist and his "inner mood". We noticed that the enamel reflects all the experiences of the master that occur during work, so one of the goals is to build a friendly process of collaboration.
After all the colors are laid, we check for fluidity - fill the product with hot water and leave it for a day. Holes invisible to the eye may occur from the tension of the metal during firing, so it is important to check and, if detected, eliminate the defect that has arisen. The dishes should not leak.
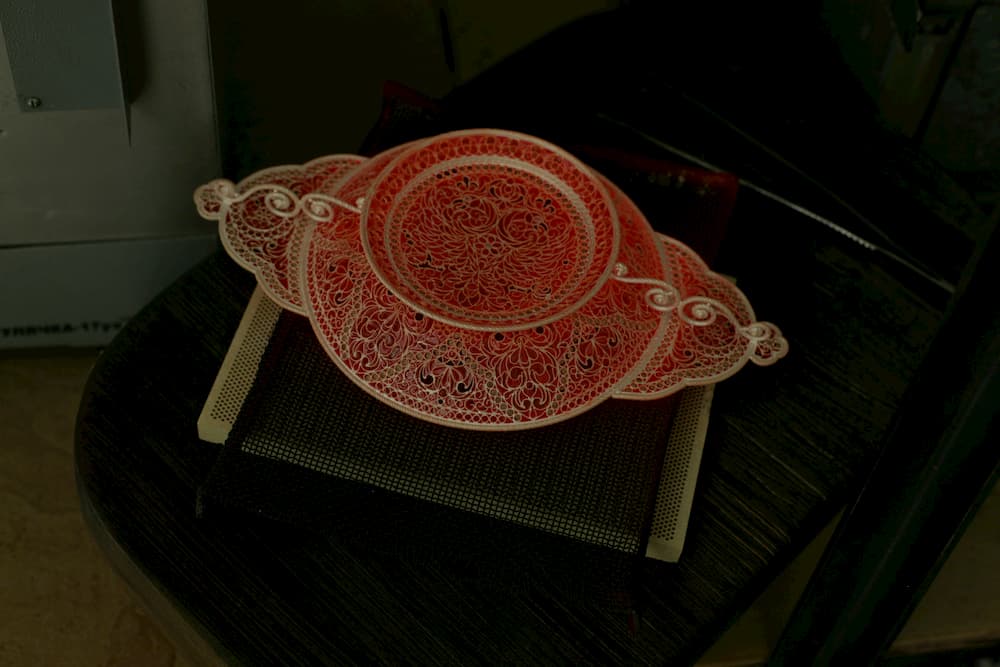
The product after firing
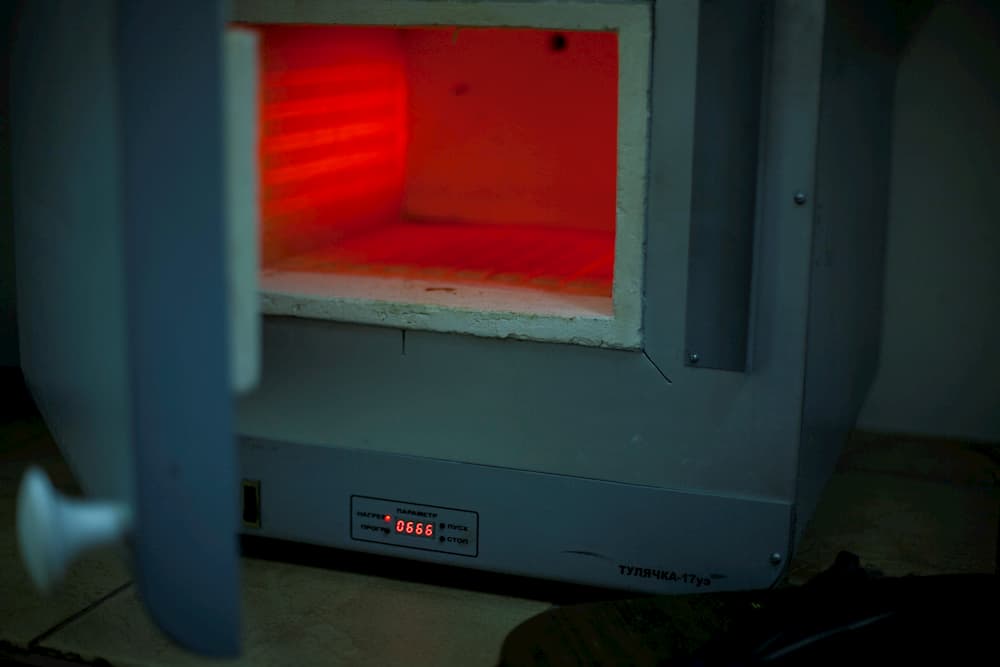
Muffle furnace
When the enameler copes with its task, the product needs additional gloss at the finishing stage. The jeweler polishes the surface of the product very carefully. One wrong hand movement can lead to a sad result. For this reason, polishing jewelry is entrusted only to experienced hands.
The final stage is the gilding of the product in an electroplating bath. Gilding gives a modern sound to the product, while, over time, becoming covered with patina, the product will take on a noble antique shade, revealing the color play of stained glass enamel.
Thus, we have generally described the process of creating a product with stained-glass enamel to understand its beauty and value. And as you can see, this is far from easy painstaking work, requiring professionalism and talent. But this does not stop us, but on the contrary, encourages us to create more and more new, complex, original and interesting things. And every time the stained-glass enamel captivates with its beauty and plays on our imagination. And the play of light, the charming iridescences of the stained-glass capture and fill the heart with delight. There is something exciting, attractive and not always descriptive about it…
Stained-glass enamel is a meeting of warm noble metal with aristocratically shimmering enamel, an amazing dance of combining the two into one…
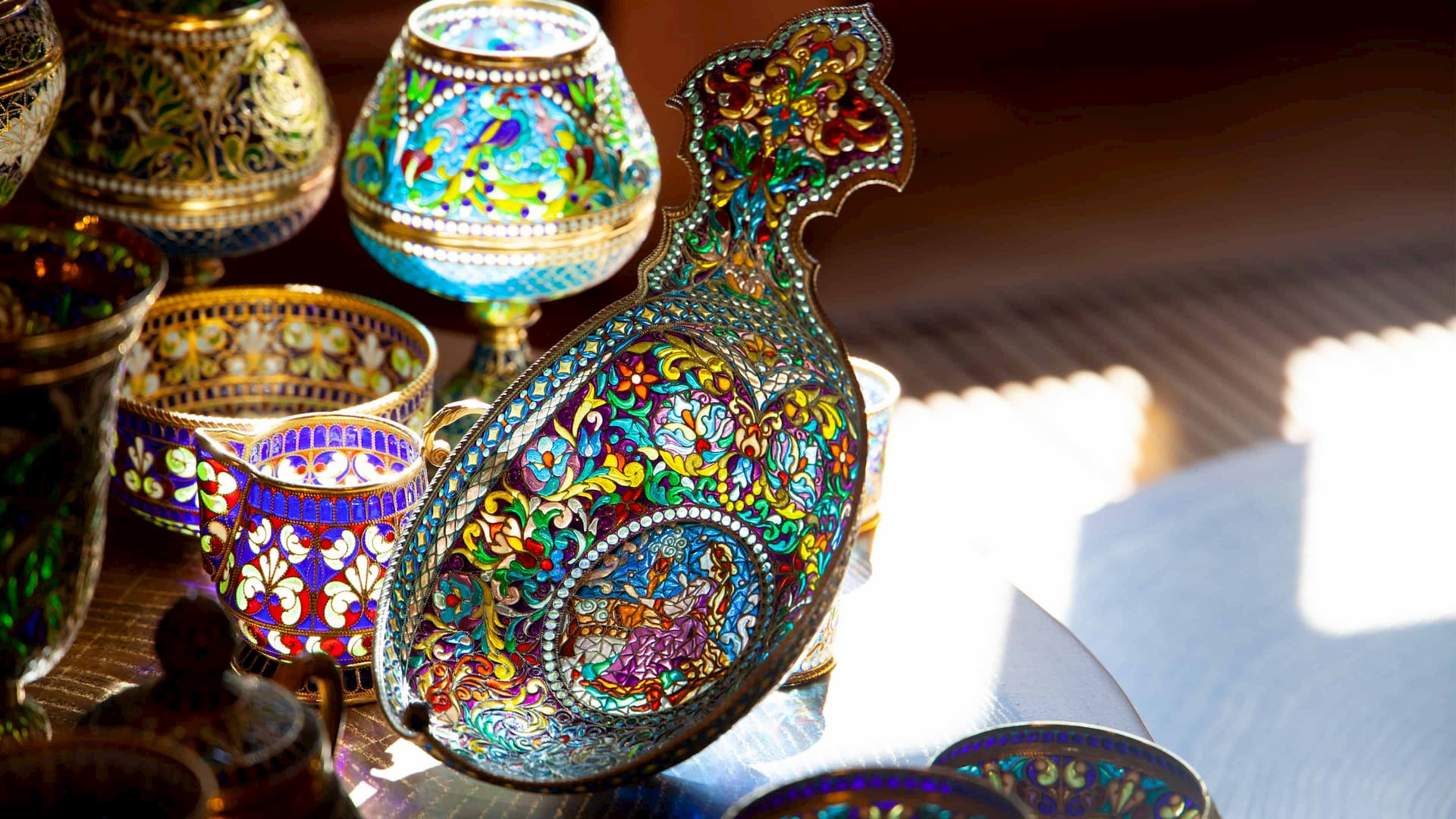