Filigree riza
Creating a frame for an icon is a very long, time-consuming and delicate process. The manufacture of a filigree riza in this process is in the first place. The filigree riza covering the icon is understood as a symbolic disclosure of the image of salvation of the soul, the shining garment of purity (silver) and Divine Grace (gold). The roza, like any other element of the frame, is individually designed by the artist, taking into account all the features of the Image presented on the icon.
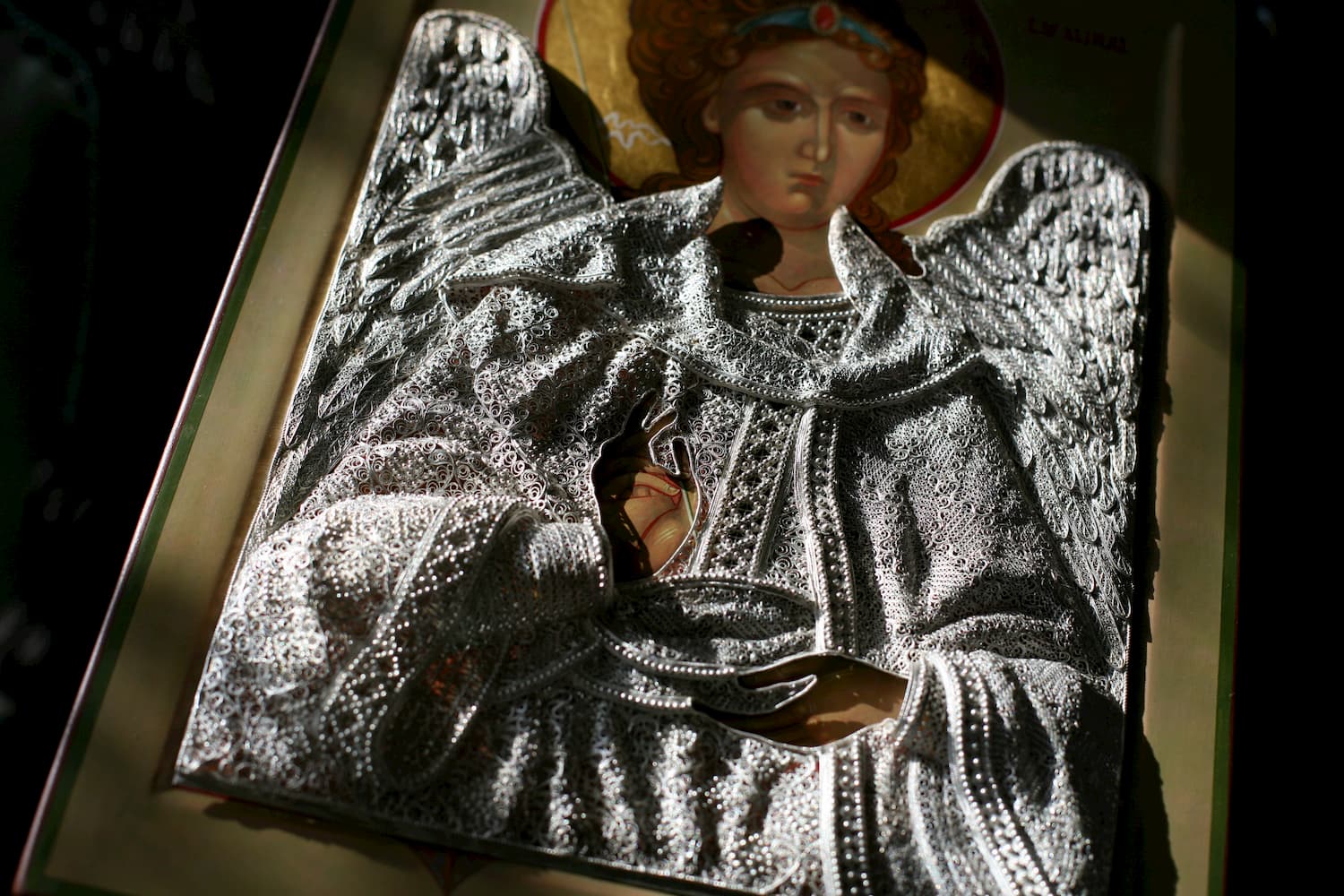
The icon of the Archangel Barachiel. The filigree riza is almost ready - the final stage of oxidation remains.
But before describing the process of creating a filigree robe, let's look at the terminology. Often, by riza we mean the entire carcass of the icon, however, a more precise definition sounds like this: a riza is a precious garment covering the clothing of the saint depicted on the icon.
To create a precious riza, we use the filigree technique, which is very similar to a filigree, and the only difference between them is in the grain. Grains are small silver balls that are soldered onto a filigree using solder. It is the connection of the grain with the filigree that forms the filigree. The execution of the filigree technique is elegant and subtle, therefore a high level of skill is required from the jeweler. It is no coincidence that the concept of filigree is used in colloquial speech to denote fine work.
The filigree effect is achieved due to the twisted wire (filigree) placed on the edge, which is rolled in flat rollers and subjected to uniform soft annealing. The wire material is 960 silver.
A metal artist sculpts a sculpture, giving a three-dimensional shape to the icon's handwriting, and transmits small details of clothing. According to the created sculpture, the master forms a pattern of flat filigree wire using jewelry tweezers and scissors. The pattern consists of thousands of elements, each of which is bent with tweezers and cut with scissors to the required length - this is a very painstaking process that requires care and perseverance, It takes several months to create a riza. Additionally, silver balls (grains) are used. The master covers all contact points with flux and applies solder, preparing the riza for soldering.
During soldering, the parts are connected by means of solder, a binder alloy, which, heating up and becoming liquid, spreads between the soldered parts and forms a strong connection. The flux is used to facilitate the entire soldering process. The melting temperature of the solder must be lower than the temperature of the silver wire, otherwise it may also melt, and the temperature of the flux is even lower than the solder temperature.
Pure silver retains its color even when heated, but the riza is made of 960 silver, which turns black when soldering, because the copper contained in it reacts with oxygen at high temperature on the surface and forms black copper oxide. When bleaching all the copper particles on the surface dissolve and our riza returns its silver color.
However, for a harmonious perception of the Image, we artificially blacken the silver using the oxidation technique. Over time, under the influence of the environment, silver becomes covered with a natural patina - the technique of plating only accelerates this process, giving the product a noble antique shade.
For all its variety and complexity of ornamental filigree interlacing, the riza does not interfere with the general perception of the Image, but only harmoniously decorates and directs to the contemplation of the icon.
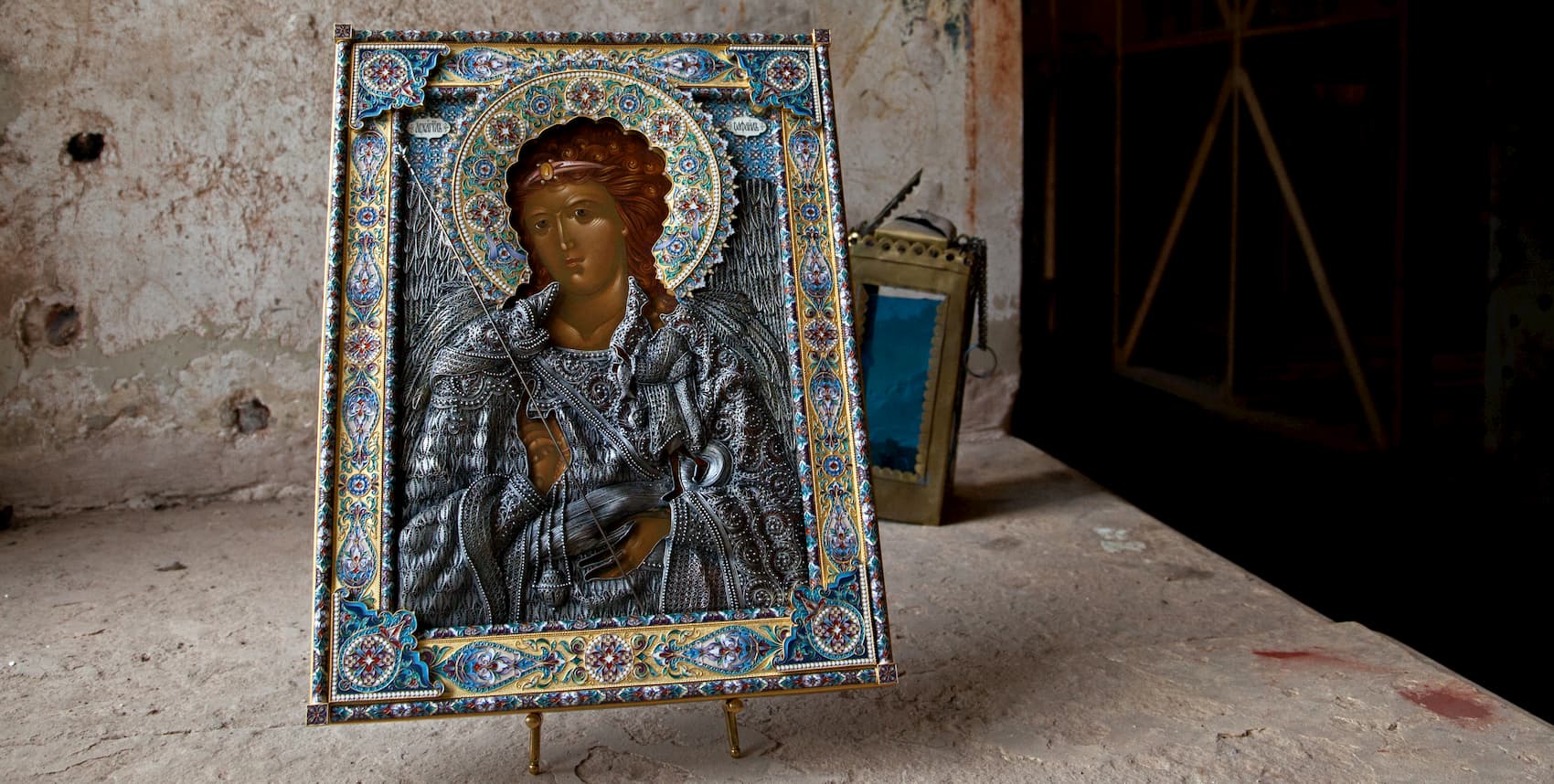
the Icon of the Archangel Raphael. The wings and vestments of the Archangel, as well as the boy Tovia with a fish in his hands, are made in the filigree technique.